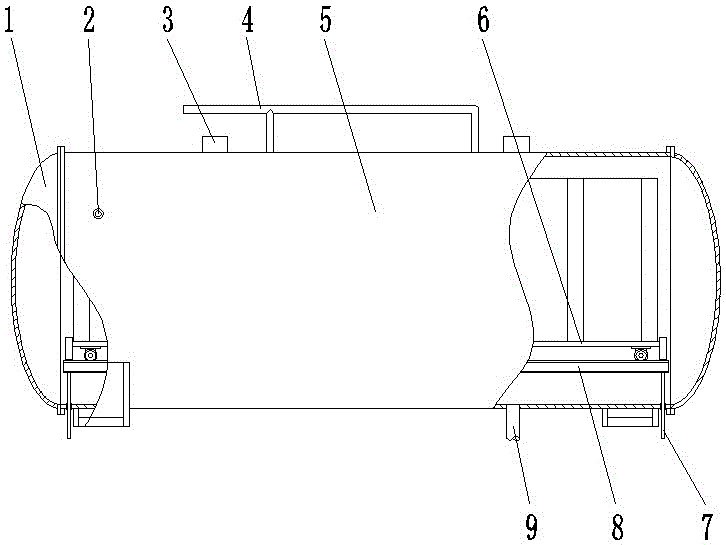
本發(fā)明涉及一種石墨化生產(chǎn)工藝和專用爐,提別是一種閉式石墨化生產(chǎn)工藝及密石墨化爐。
背景技術(shù):
:目前石墨制品的石墨化主要采用的是艾奇遜石墨化爐和串接石墨化爐,上述兩種石墨化爐各有特點,但由于其在石墨化生產(chǎn)過程中是采用開放式的常壓生產(chǎn),一方面造成爐子運行期間有大量的有害氣體逸出,如CO、CO2等,作業(yè)環(huán)境較差;另一方面生產(chǎn)過程中的熱效率只有30%—35%,如果再把20%多的電損失計算進去,能量利用的總效率就只有23%—28%;第三,由于石墨化過程是在常壓下進行,石墨化制品中的碳原子晶格結(jié)構(gòu)無法人為改變,同時在石墨化過程完成后爐料自然冷卻過程中,大量析出的有害揮發(fā)物質(zhì)會在冷卻過程中,吸附在石墨化制品表面,造成石墨化制品表面的灰分上升,機械強度降低。技術(shù)實現(xiàn)要素:本發(fā)明的目的是解決現(xiàn)有技術(shù)存在的缺陷,提供一種可人為控制石墨化過程的反應(yīng)氛圍和壓力,可有效提高石墨制品品質(zhì)、降低生產(chǎn)過程中對環(huán)境污染的密閉式石墨化爐。1.本發(fā)明的技術(shù)方案是:一種密閉式石墨化生產(chǎn)工藝,該工藝步驟為:1)裝爐:在可移動爐槽車底板兩端安裝好石墨電極爐墻后,在兩石墨電極爐墻之間的可移動爐槽車底板上鋪一層硅石顆粒,然后在硅石顆粒上鋪一層冶金焦顆粒,將需要石墨化的碳素制品順序放置在冶金焦顆粒層上,然后用石墨粉將碳素制品之間和碳素制品與兩石墨電極爐墻之間的縫隙充填好之后,在需要石墨化的碳素毛坯上順序鋪一層冶金焦顆粒和硅石顆粒;2)煅燒:將裝填完成的可移動爐槽車推入密閉式石墨化爐內(nèi),使可移動爐槽車兩端的石墨電極爐墻上的石墨電極與承壓釜兩端的電極母線聯(lián)通,同時將電極母線上的冷卻水套與承壓釜上的循環(huán)水進、排水管接通,關(guān)閉承壓釜一端或兩端的封頭后,抽真空排出承壓釜內(nèi)的空氣,然后向承壓釜內(nèi)注入惰性氣體后,開始通電煅燒;3)卸料:石墨化結(jié)束后,打開承壓釜一端或兩端的封頭,將可移動爐槽車從承壓釜內(nèi)拉出進行卸料,并將硅石顆粒和冶金焦顆粒粉篩后備用。上述硅石顆粒的粒度為2-10mm;上述冶金焦顆粒的粒度為12-30mm。在上述煅燒步驟中,向承壓釜內(nèi)注入惰性氣體后通電煅燒的具體工藝過程是:通電煅燒時,當承壓釜內(nèi)的壓力達到0.3—0.7KP時,打開承壓釜上的排氣閥使承壓釜內(nèi)的壓力至常壓后關(guān)閉排氣閥,抽真空使承壓釜內(nèi)保持1KP以上的負壓,并持續(xù)5-10小時后停止抽負壓,通過承壓釜上的壓力控制閥保持承壓釜內(nèi)的壓力在0.1—0.4MPa的正壓下煅燒40-45小時后斷電;當承壓釜內(nèi)的壓力降到常壓后,向釜內(nèi)注入氮氣,用氮氣將承壓釜內(nèi)的反應(yīng)后的氣體置換掉;當承壓釜內(nèi)的溫度至常溫后,打開將承壓釜一端或兩端的封頭,將可移動爐槽車從承壓釜內(nèi)拉出進行卸料。一種密閉式石墨化爐,包括一端或兩端可開啟的密閉的承壓釜,在承壓釜上安裝有進氣管、排氣管、壓力控制閥和安全閥,其特征在于在承壓釜內(nèi)固定安裝有水平導(dǎo)軌,在承壓釜兩端安裝有與承壓釜密閉、絕緣的電極母線,電極母線的一端在承壓釜內(nèi),另一端與供電系統(tǒng)相連,石墨化過程中可移動爐槽車裝在承壓釜內(nèi);上述可移動爐槽車是由車底板、固定安裝在車底板上的滾輪、安裝在車底板上的立柱、安裝在兩立柱之間的護墻板和裝在可移動爐槽車兩端的石墨電極爐墻組成,在車底板兩端安裝有與上述電極母線相配的母線連接裝置。在上述承壓釜兩端安裝有進、排水管。上述承壓釜的截面為圓形也可為橢圓形或多邊形;上述可移動爐槽車上的立柱為可拆卸式的圓弧形或多邊形。上述車底板兩端安裝有與上述電極母線相配的連接裝置為刀閘。上述裝在可移動爐槽車兩端的石墨電極爐墻是由保溫磚和石墨電極組成,石墨電極設(shè)置在石墨電極爐墻的中部。本發(fā)明的技術(shù)方案是將現(xiàn)有的石墨化過程由常壓改為在全封閉承壓釜內(nèi)進行,這樣就可人為控制承壓釜內(nèi)的石墨化氛圍,提高石墨制品的密度和純度,從而提高制品的強度和性能。由于石墨化焙燒過程是在密閉環(huán)境中進行,可根據(jù)不同碳素制品的需要,控制承壓釜內(nèi)的反應(yīng)氛圍和壓力,同時完成對不同材料進行冶煉、還原、煅燒、復(fù)合或提純的工藝技術(shù)。為本工藝提供的專用密閉的承壓釜,是由承壓釜和可移動爐槽車組成。通過控制承壓釜上的進氣管和排氣管打開與關(guān)閉,可控制釜內(nèi)的壓力,使石墨化過程中碳素的晶體結(jié)構(gòu)有序排列,提高了制品的強度;通過進氣管向釜內(nèi)通入惰性氣體和抽負壓等方式改變釜內(nèi)的反應(yīng)氛圍,可使碳素中的鈣、鎂、鋁、鐵等雜質(zhì)的蒸發(fā)溫度降低,有效提高石墨制品的純度和強度;裝料和卸料是在承壓釜外的可移動爐槽車上進行,可有效降低生產(chǎn)周期和可承壓釜的利用率;利用排氣管將石墨化過程中的有害氣體集中收集,可有效降低環(huán)境污染。附圖說明附圖1為本發(fā)明的結(jié)構(gòu)示意圖;附圖2為本發(fā)明附圖1的左視剖面圖;附圖3為本發(fā)明可移動爐槽車的結(jié)構(gòu)示意圖;附圖4為本發(fā)明附圖3的左視圖;附圖5為本發(fā)明附圖3的A-A剖視圖。具體實施方式在附圖1-4中,1-封頭、2-進、排水管、3-安全閥、4-排氣管、5-承壓釜、6-可移動爐槽車、6-1-連接座、6-2-車底板、6-3-滾輪、6-4-固定立柱、6-5-護墻板、7-電極母線、8-水平導(dǎo)軌、9-進氣管、10-硅石顆粒、11-冶金焦顆粒、12-石墨粉、13-碳素毛坯。下面就本發(fā)明技術(shù)方案的工藝步驟及專用設(shè)備詳細說明如下:實施例1:1)裝爐:在可移動爐槽車底板兩端安裝好石墨電極爐墻后,將石墨電極爐墻上的石墨電極通過電極母線與可移動爐槽車兩端的母線連接裝置相連。然后在兩石墨電極爐墻之間的可移動爐槽車底板上鋪一層粒度為2mm硅石顆粒,然后在硅石顆粒上鋪一層粒度為12mm冶金焦顆粒,將需要石墨化的碳素制品順序放置在冶金焦顆粒層上,然后用石墨粉將碳素制品之間和碳素制品與兩石墨電極爐墻之間的縫隙充填好之后,在需要石墨化的碳素毛坯上順序鋪一層冶金焦顆粒和硅石顆粒;硅石顆粒主要起隔熱保溫作用;冶金焦顆粒主要起導(dǎo)電、加熱作用;石墨粉的作用是使需要石墨化的各碳素毛坯之間和墨電極爐墻之間形成電連接。3)煅燒:將裝填完成的可移動爐槽車推入密閉式石墨化爐內(nèi),使可移動爐槽車兩端的母線連接裝置與承壓釜兩端的電極母線連接好,該鏈接可以通過刀閘或其他現(xiàn)有技術(shù)的連接方式,其目的是將可移動爐槽車兩端與承壓釜兩端的電極母線之間建立可拆卸的電連接。同時將電極母線上的冷卻水套與承壓釜上的循環(huán)水進、排水管接通,對電極母線進行冷卻,然后關(guān)閉承壓釜一端或兩端的封頭后,抽真空排出承壓釜內(nèi)的空氣后,向承壓釜內(nèi)注入惰性氣體,開始通電煅燒;當承壓釜內(nèi)的壓力達到0.3KP時,打開承壓釜上的排氣閥使承壓釜內(nèi)的壓力至常壓后關(guān)閉排氣閥,抽真空使承壓釜內(nèi)保持1KP以上的負壓,并持續(xù)10小時后停止抽負壓,通過承壓釜上的壓力控制閥保持承壓釜內(nèi)的壓力在0.1MPa的正壓下煅燒45小時后斷電;當承壓釜內(nèi)的壓力降到常壓后,向釜內(nèi)注入氮氣,用氮氣將承壓釜內(nèi)的反應(yīng)后的氣體置換掉;當承壓釜內(nèi)的溫度至常溫后,打開將承壓釜一端或兩端的封頭,將可移動爐槽車從承壓釜內(nèi)拉出,進行卸料,在卸料后,將硅石顆粒和冶金焦顆粒進行篩分,備下次使用。實施例2-3。實施例2、3如下表,在上述實施例中,改變硅石顆粒、冶金焦顆粒的粒度和煅燒壓力、時間,其他工藝條件不變。實施例硅石粒度冶金焦粒度煅燒壓力煅燒壓力26mm20mm0.4KP、8小時0.4MPa、40小時310mm30mm0.7KP、5小時0.2MPa、42小時在上述實施例中硅石顆粒、冶金焦顆粒的鋪設(shè)厚度根據(jù)具體情況進行確定,一般在40—50厘米左右。在上述任意實施例中,所采用的密閉式石墨化爐的結(jié)構(gòu)如圖1-5所示,密閉式石墨化爐是由一端或兩端可開啟的密閉的承壓釜和裝在密閉的承壓釜內(nèi)的可移動爐槽車組成;在承壓釜上安裝有進氣管9、排氣管4和安全閥3,在承壓釜內(nèi)固定安裝有水平導(dǎo)軌8,在承壓釜兩端安裝有與承壓釜密閉、絕緣的電極母線7,電極母線的一端在承壓釜5內(nèi),另一端與供電系統(tǒng)相連;可移動爐槽車是由車底板6-2、固定安裝在車底板上的滾輪6-3、安裝在車底板上的立柱6-4、安裝在兩立柱之間的護墻板6-5和裝在可移動爐槽車兩端的石墨電極爐墻10組成,在車底板兩端安裝有與上述電極母線7相配的母線連接裝置6-1,該母線連接裝置可采用刀閘或其它電連接形式;上述石墨電極爐墻是由保溫磚和放置在石墨電極爐墻的中部的石墨電極11和一端與石墨電極電連接、另一端與母線連接裝置電連接的導(dǎo)電母線組成。使用時,先將需要石墨化的制品和保溫料裝在可移動爐槽車內(nèi),制品兩端通過粉狀石墨與石墨電極爐墻上的石墨電極內(nèi)側(cè)相連接,石墨電極外側(cè)通過導(dǎo)電母線與母線連接裝置連接,裝好需要石墨化的物料后將可移動爐槽車推入承壓釜內(nèi),將可移動爐槽車兩端的母線連接裝置與承壓釜兩端的進線母線連接好后,將承壓釜兩端的封頭1與承壓釜密閉,即可通電對釜內(nèi)可移動爐槽車上的制品進行石墨化。根據(jù)承壓釜的截面設(shè)計立柱的形狀,主要目的是提高可移動爐槽車的裝料量。當承壓釜的截面為圓形時,可移動爐槽車上的立柱可制作為圓弧形,并且為方便裝卸料,立柱與可移動爐槽車的車底板之間設(shè)計為可拆卸連接方式,如插接形式。當承壓釜的截面為橢圓形或多邊形時,立柱可設(shè)計為圓弧形或多邊形。為防止可移動爐槽車兩端與電極相連的導(dǎo)電母線在高溫狀態(tài)下被燒損,在承壓釜兩端安裝有進、排水管2,通過水套給電極母線降溫。在石墨化過程中產(chǎn)生的有害氣體,則通過排氣管4收集利用。當需要承壓釜內(nèi)的石墨化過程為正壓時,將進氣管、排氣管關(guān)閉,就可實現(xiàn)釜內(nèi)正壓。當需要承壓釜內(nèi)負壓時,關(guān)閉排氣管,同時將進氣管與真空泵連接,通過真空泵將承壓釜內(nèi)的氣體抽出,就可實現(xiàn)承壓釜內(nèi)的負壓反應(yīng)。正壓、負壓的壓力可以根據(jù)工藝需要進行設(shè)定。同時根據(jù)不同制品的工藝需要,可以通過進氣管向承壓釜內(nèi)送入惰性氣體,如氮氣、氬氣等。當前第1頁1 2 3